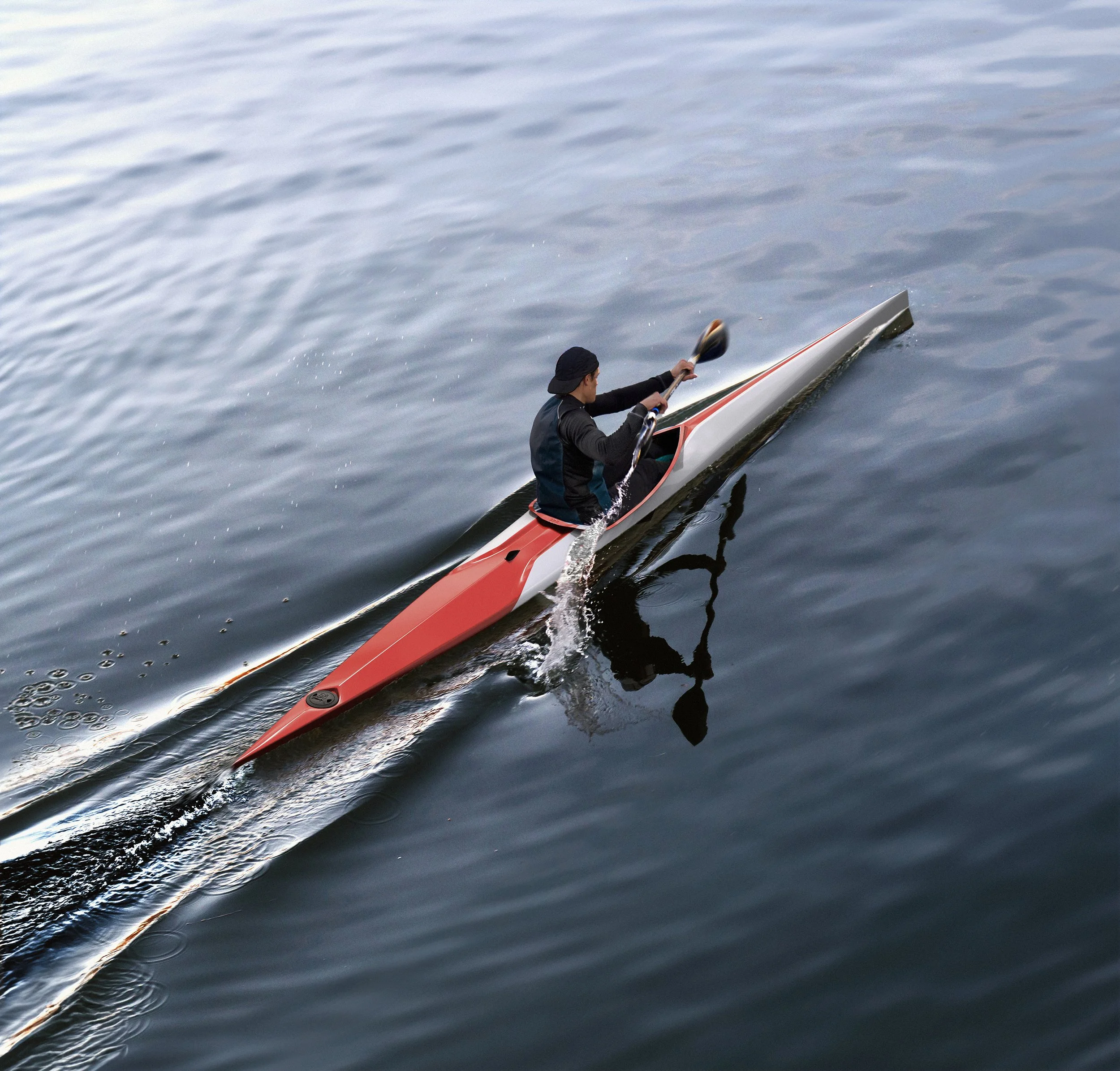
D46
Touring & Racing Kayak
Product Development
for Subkayak Composites
ROLE
Lead Industrial Designer
YEAR
Q1-Q3 2023
CLIENT
Subkayak Composites
SERVICES
Creative Direction
Industrial Design
Reverse Engineering
CAD
Prototyping
The D46 is suitable for both racing and touring. It provides exceptional speed with a modern and distinctive style, exciting two-color base version and customisable 3D printed components.
My responsibility was to lead the complete product development process, from concept design and reverse engineering, to the technical realisation of the CAD file ready for manufacturing.
The project was honoured with an exhibition spot at the 2023 Hungarian Design Awards, it received enthusiastic feedback and generated substantial orders post-launch.
The design of the D46 creates an impression of being divided into two sections, suggesting a core surrounded by a shield on the front section of the body.
The dynamic, sculptural forms, complemented by the paintwork, play a key role in accentuating this two-part effect, which gives the D46 its recognisable character.
Reverse Engineering
►
Concepts
►
3D Draft Models
►
CAD
►
3D printing
►
🏁 Build Kayak 🏁
⚪️
Reverse Engineering ► Concepts ► 3D Draft Models ► CAD ► 3D printing ► 🏁 Build Kayak 🏁 ⚪️
1.
REVERSE ENGINEERING
The development began with reverse-engineering the hull of the client's hand-built kayak, initiating a precise 3D scan. This step was crucial to accurately preserve the kayak's optimal hydrodynamic properties and ensure that the new design maintained the performance characteristics of the original reference model.
2.
CONCEPT SKETCHING AND 3D MODELING
After the successful completion of the rebuilt surface, it formed the foundation for the next stages. This phase resulted in the creation of 3D volume models that integrated all design features from my concept sketches. Once the design was refined in these 3D models, the next step involved advancing to the development of the final CAD file.
3.
CONCEPT SKETCHING AND 3D MODELING
In this phase, a distinct focus was placed on A-class surface modeling to ensure a seamless and high-quality surface finish. This precision was key for CNC machining a 1:1 scale foam model of the kayak. Adopting this approach effectively removed the need for expensive physical prototypes and many hours of manual labor to correct any surface imperfections. It allowed for a smooth transition from the CAD design directly to production, streamlining the entire process.
GALLERY


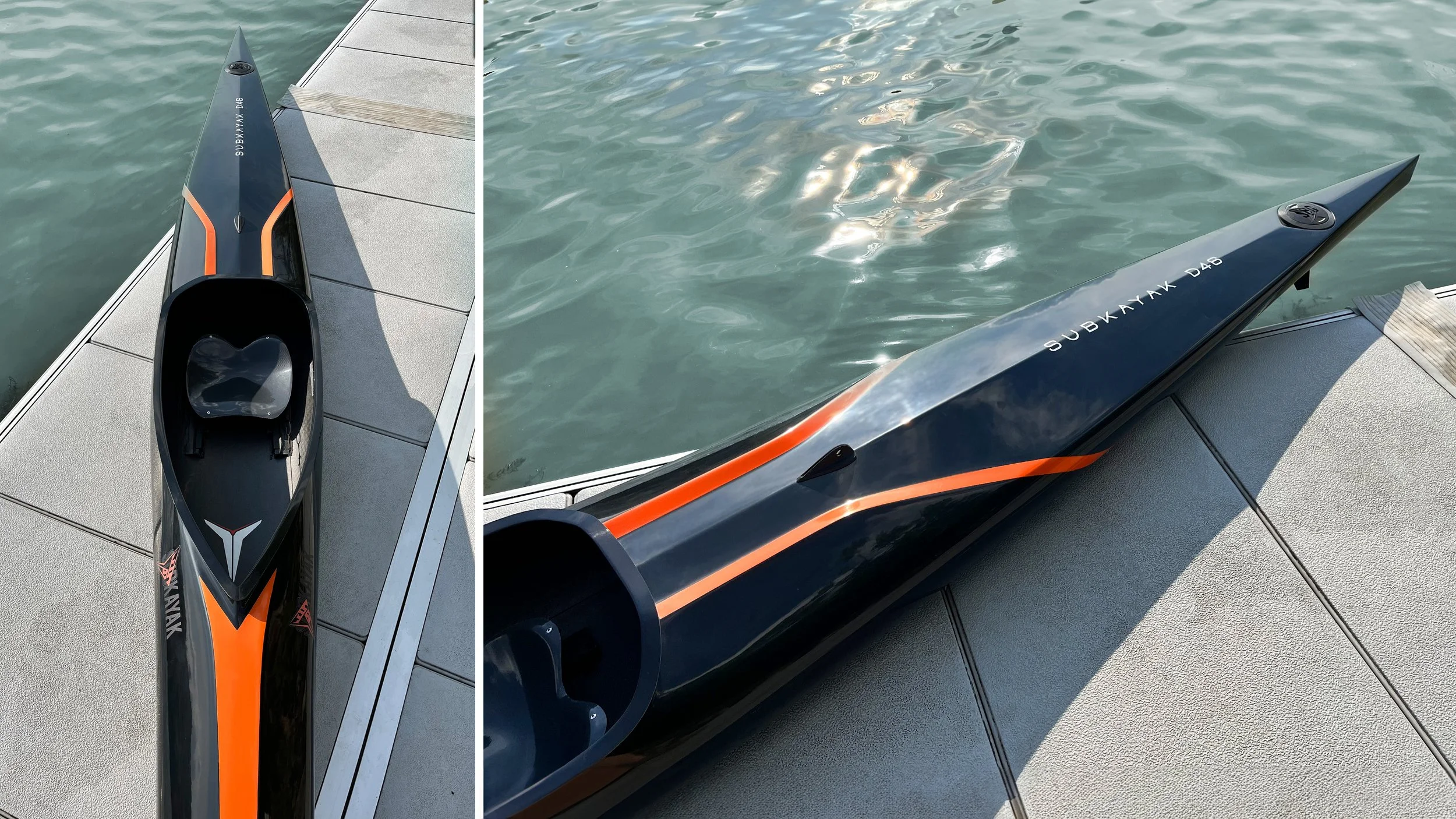
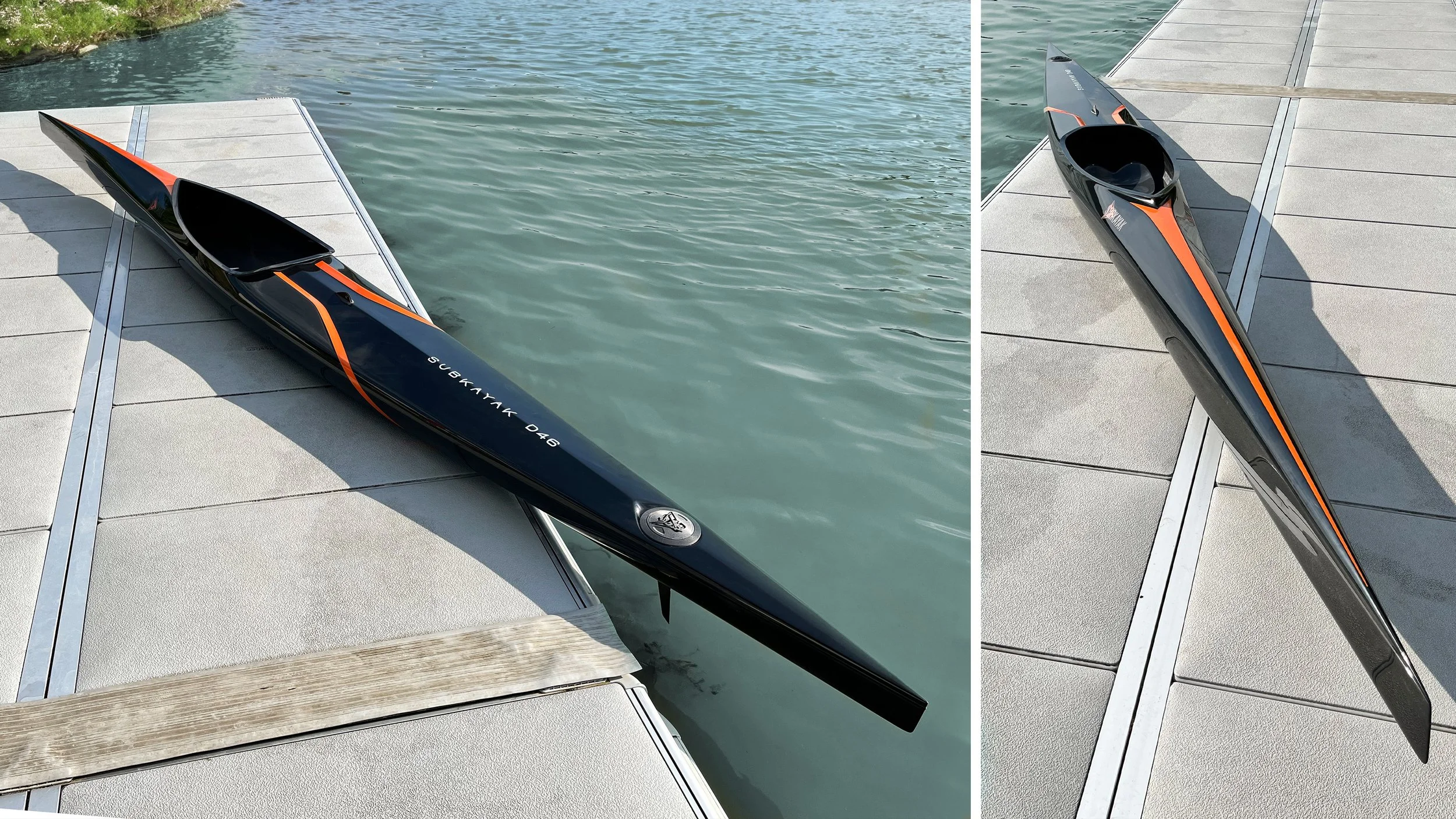
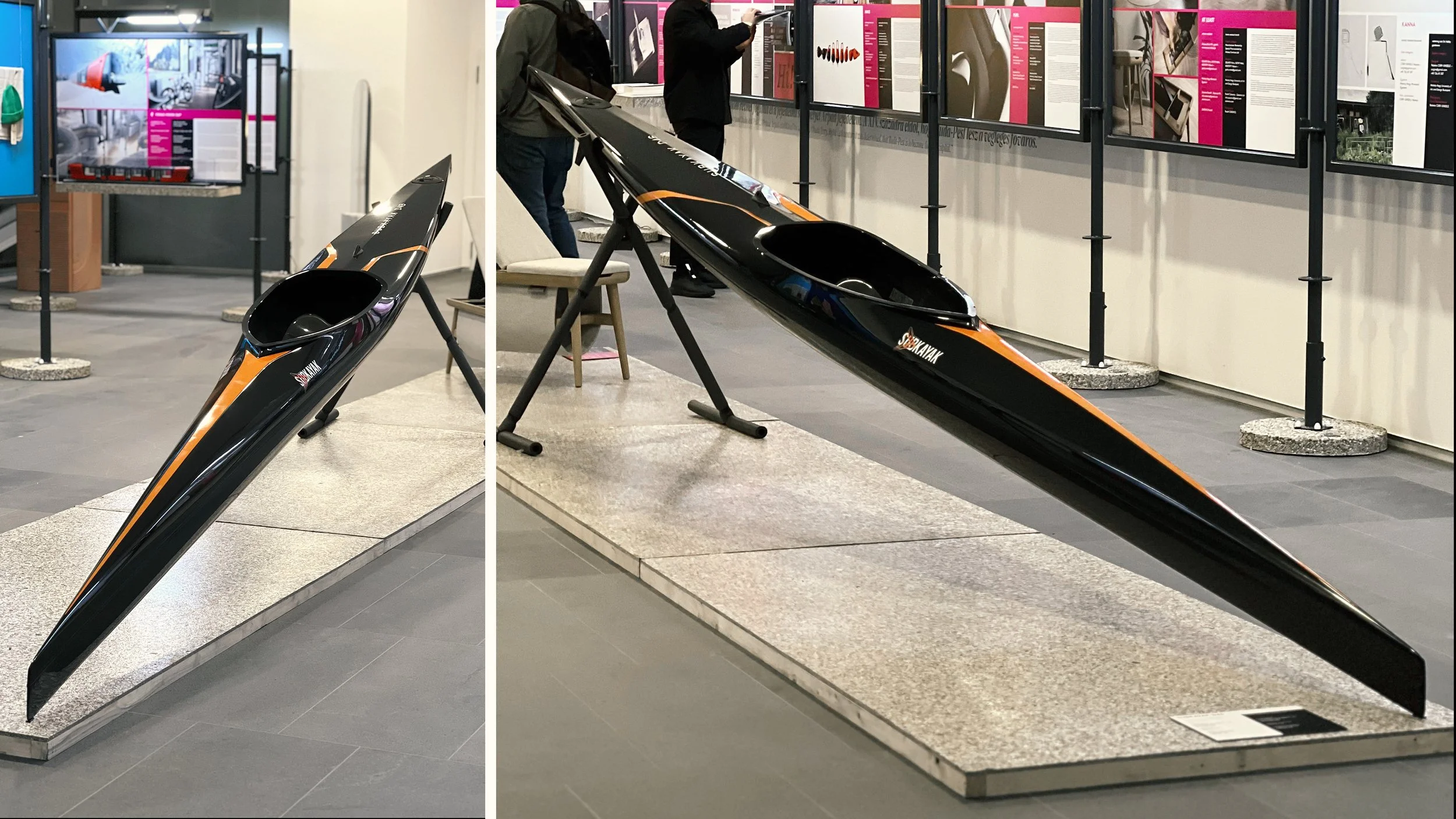
Interested in a
similar project?
From Concept to Technical realisation. Let's Work Together!